The History of Orbital Tube Welding
The year was 1957. Walter Spivak, the chief engineer at North American Aviation’s Los Angeles Division, convened a meeting to discuss the X-15 Rocket Research plane. The X-15 was designed to fly at speeds of 4,500 miles per hour and reach altitudes of over 350,000 feet to investigate all aspects of piloted hypersonic flight.
Invited to the meeting were representatives from several of the design and manufacturing departments. Also attending the meeting was legendary test pilot Scott Crossfield. Scott would be the first pilot to fly the cutting edge plane. Scott was in the meeting to express his concern about fuel and hydraulic fluids weeping and leaking in and around the plumbing of the 12,000-pound thrust rocket engine. There were about 30 engineers and others lining the walls in a horseshoe shape around the conference room. After Crossfield made his plea to fix the potentially catastrophic leaks, Spivak asked if there were any ideas on how to solve this very serious problem. After what seemed like an eternity, Rod Rohrberg a member of the producibilities group, blurted out “Why don’t we Automatically Weld It”. This stunned his contemporaries as Rod was only 32 years old and had yet to distinguish himself at North American.
It took Rod about 3-4 weeks to design and fabricate the first test unit. The proof of concept welding apparatus was a crude devise that utilized a Bridgeport mill for the drive mechanism. A stationary tube was mounted in an insulated housing. The housing contained a race track that had an electrode shuttle mounted in it. The shuttle had a power cable attached to it, with the other end connected to a power supply. The housing was mounted to the mill table and the power cable was attached to the mill spindle. The electrode moved around the tube by turning the X-axis handle away from the spindle. This moved the housing away from the spindle and in turn pulled the shuttle around the tube. The housing also served as a means to contain the argon gas and provide a ground path.
It took several attempts to strike and maintain an arc. Once the arc was stable, Rod turned the mill handle and pulled the electrode around the tube making the first in place orbital weld. With this crude devise Rod validated his vision of making an automatic weld.
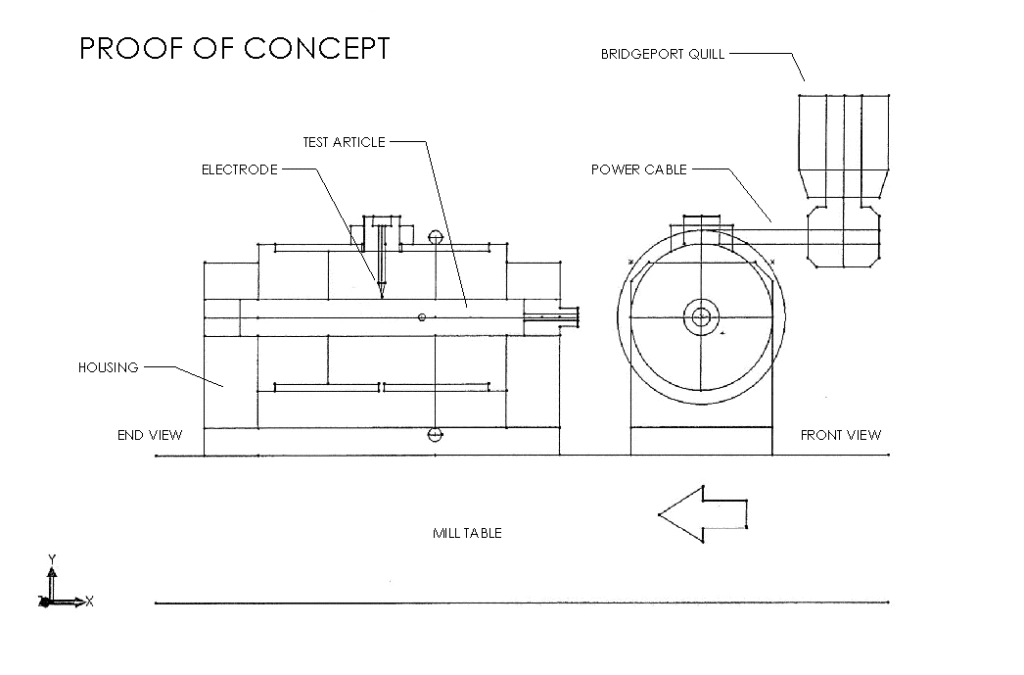
Rod made this proof of concept weld on October 4, 1957. This was a stark reminder of the cold war, as this was the same day that the Soviet Union launched the first artificial satellite named Sputnik into low earth orbit. This launch ran chills through the Pentagon and all of Washington DC, as this meant that the Soviets could replace Sputnik with a nuclear weapon.
Now the hard work begins.
There were many challenges to overcome. Rod needed to design; a clamping system to hold the tube ends together, a way to hold the electrode (rotor) and orbit it around the tube while maintaining a constant arc gap, had to supply an uninterrupted flow of power to the rotor, design the rotor that will allow the welded tube to be removed from the fixture, insulate the power from the ground, contain the argon purge gas, design a drive system. All of this while designing the holding fixture small enough to fit in the restricted areas in and around the engine and fuselage.
It was also being closely monitored by NASA, department of the Air Force, department of the Navy and other interested parties. There was a tremendous amount of pressure on Rod and North Americans management to perform as expectations were high on this new possibility.
Designing the prototype was like an intricate dance. Every feature interacted with every other feature like a ballroom dance. If one feature was out of step with its partner(s), the system would not operate to the full potential that automatic tube welding was thought to possess. Unfortunately this effort began too late to be used on the X-15. Once North Americans management and customers saw the possibilities of this new process, they kept Rod busy with new and more difficult applications. When it became apparent that automatic welding would not be ready for the X-15, Rod also developed in-place induction brazing to reduce the number of weeps and drips in the X-15. Brazing, while less desirable than welding, was way easier to develop as it doesn’t have any moving parts. Rod learned a great deal and overcame many obstacles while designing the prototype, however it did not contain an integral drive motor. The drive system contained everything to rotate the electrode around the tube but the motor. Rod used an external motor to run the prototype head. To incorporate an integral motor at this point would necessitate a major redesign. On March 30, 1962 North American filed for a patent on the first “Automatic Tube Welder”. In patent language, it was titled “Welded Connection, Method and Means”. Let there be no doubt, this was the first Orbital Weld Head!
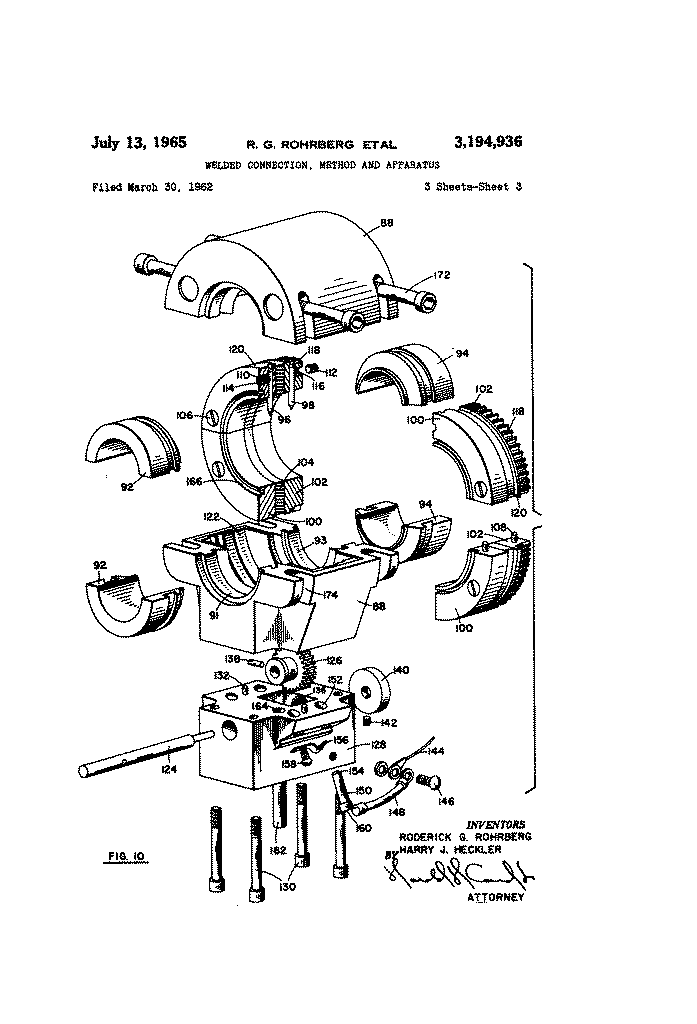
The original Orbit Arc Promotional Video filmed by North American Aviation’s Marketing subsidiary, NAVAN Products Incorporated.
What originally started out as a way to mitigate fluid leaks around a rocket engine, orbital welding turned out to be much, much more. By welding the tubular system, you could substantially reduce the number of flared couplers, tees, elbows and swaged components in fuel, hydraulic and oxygen systems. What Rod had not initially contemplated was the overall system size reduction, the tremendous weight savings and increased structural integrity.
Rod took what he learned while developing the prototype and started designing the next generation Orbital Welding Head. He designed it to be more user friendly and versatile than the prototype. This weld head had two major components in it: An upper and lower clamp that held the tube ends, contained the electrode rotor and housed the argon gas, and a removable handle that contained the drive motor, power, ground and motor control cables and a gas hose. NAA also developed the first orbital welding power supply and programming unit.
Rod named this system the “Orbit Arc Welder”
Orbit Arc had a family of weld heads and drive handles that covered a range of sizes from .250 to 4.00
While the X-15 was the plane that automatic welding was being developed for, the XB-70 Tri-Sonic Bomber was the first platform to have wide spread use. The Orbit Arc Tubular Welding System saved over 3,000 pounds of weight in the Valkyrie. That’s 3,000 extra pounds of fuel or more weapons.
Because of this achievement, Rod was named the nationwide winner of the first “Airco Welding Award” This award is conferred annually to the individual who shows the greatest originality and innovation in new products through the use of welding techniques. Rod was also the subject of many articles in North Americans “Skywriter” newsletter detailing many of his achievements.
The development of the Orbit Arc Welder was also cited by then Secretary of the Air Force, Eugene Zuckert, as one of 17 examples of important contributions made to Aeronautical Technology and Space and Launch Vehicles.
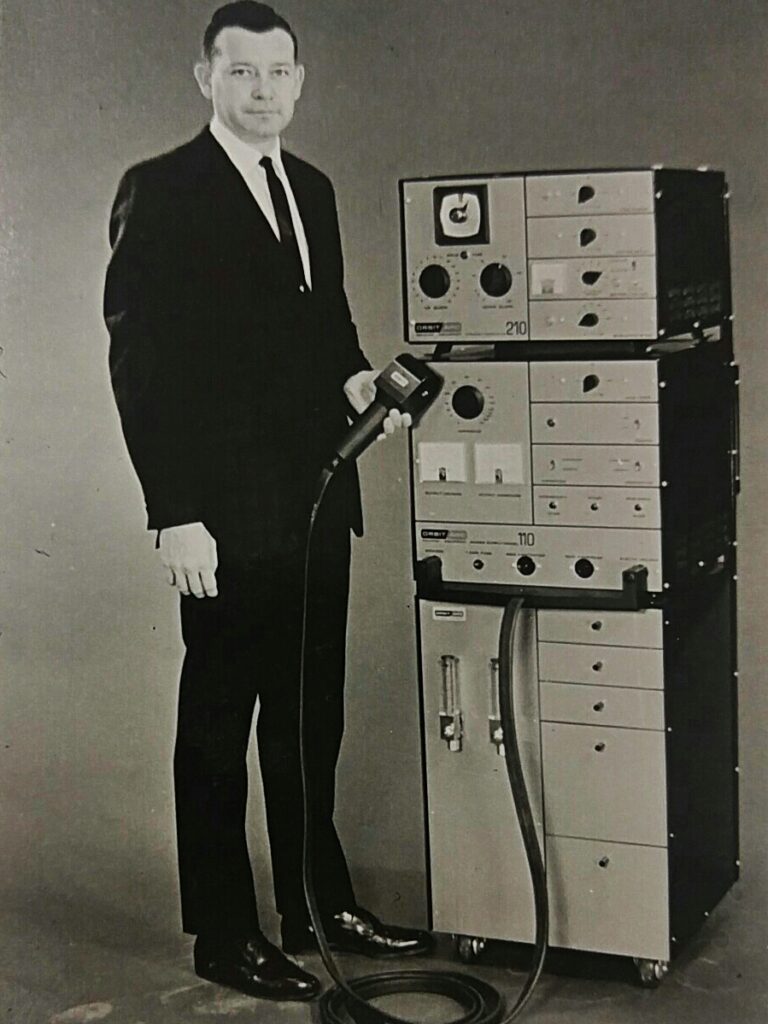